SR -120 ~ +250°C Temperature Control Systems for Multi Reactors
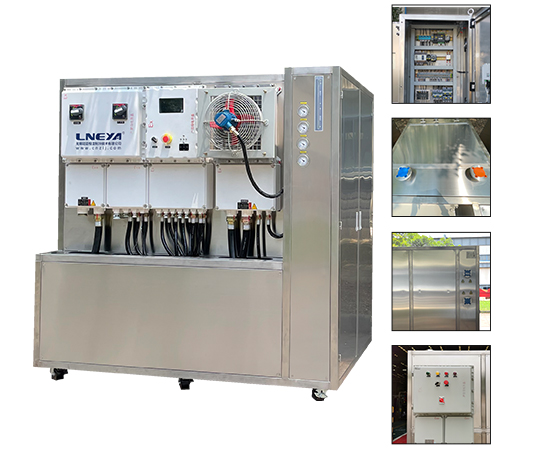
Features of Cooling and Heating Systems
- Previously unachievable performance.
- Intelligent temperature control system.
- Maximum process stability and reproducibility.
- Adop plate heat exchager, Pipeline heating, the fastest heating and cooling rates.
- High cooling power from 0.5 to 1200kW.
- Large temperature range without fluid change.
- Closed system, extend thermal fluid lifetime.
- Incredibly compact.
- 7-inch, 10-inch color TFT touch screen display.
- Comprehensive warning and safety functions.
- Rapid cooling down from high temperature.
- Use magnetic drive pump, solve the circulation pump leakage.
Advantages of Cooling and Heating Systems
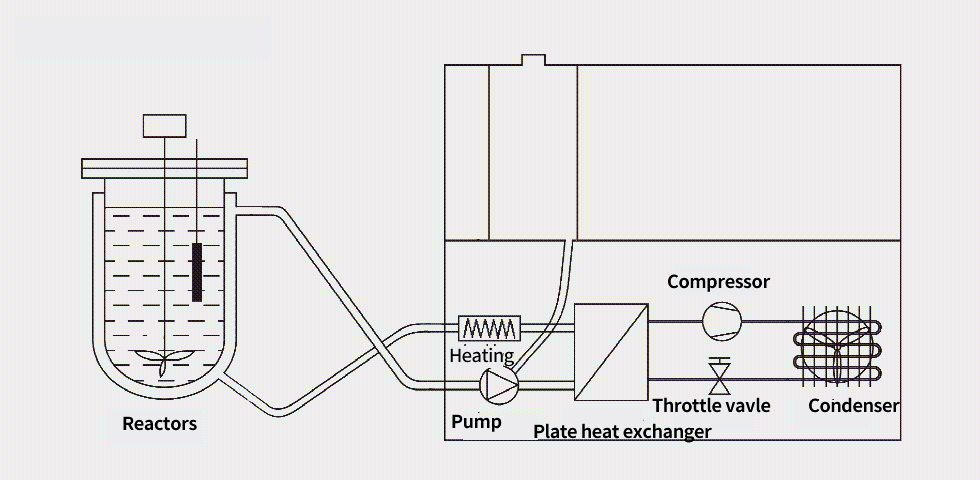
Structure Design
A fully closed piping design, high efficiency plate heat exchanger used to reduce the demand for the thermal fluid utilization while providing the system to achieve the rapid ups and downs in temperature.
The whole system is a closed liquid circulation system with the expansion of container, expansion of the container and the liquid circulation is adiabatic, and do not participate in liquid circulation, only mechanical connection, regardless of the temperature is a high temperature or low temperature, the tank temperature is limited to 60℃.
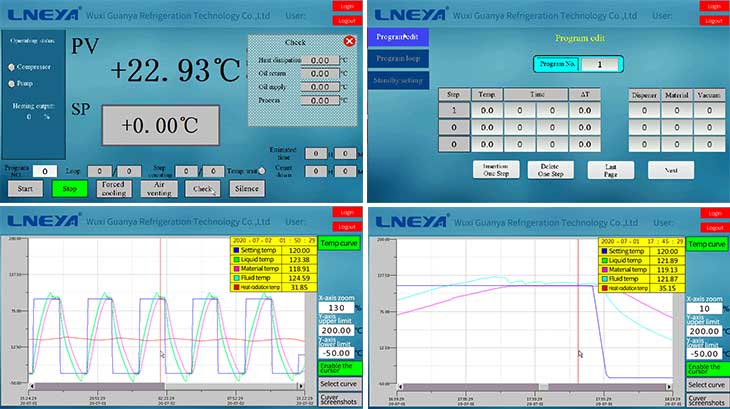
Display Function
- Display all the kind of process control temperatures.
- Shows the liquid level of the heat conducting medium in the expansion vessel.
- Shows indication for refrigeration system working.
- Shows indication for heater working.
- Shows indication for circulation pump working.
- Display the temperature control.
- The temperature upper limit, lower limit control can be set.
- The temperature difference between jacket & reactor material can be set.
- Shows the alarm to add the liquid when it is empty.
- The refrigeration compressor can be set to operate manually or automatically.
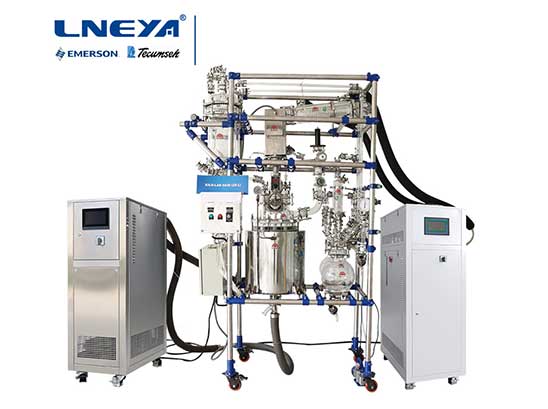
Data Interface and Software
Standard configuration:
- PT100 temperature sensor input interface.
- USB export data interface.
- RS485 communication interface (MODBUS protocol).
- Alarm output
Optional:
- 4 ~ 20mA Input interface for temperature measurement.
- 4 ~ 20mA Input interface for setting temperature.
- Ethernet interface.
- RS232 communication interface (MODBUS protocol).
- Profibus-DP interface.
- Computer operation software (optional Ethernet interface).
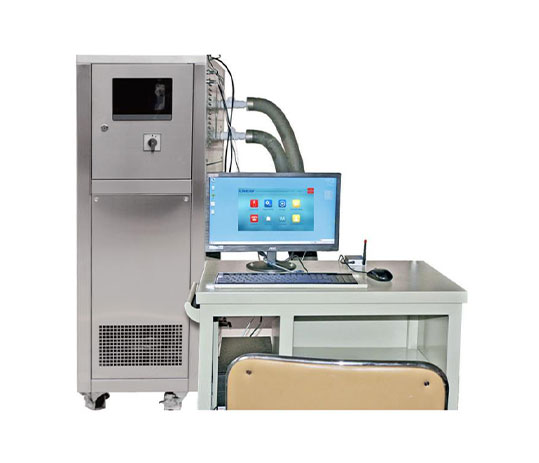
Configuration Software (Optional)
All dynamic temperature control system can be connected with the computer.
You can install and record the picture of display on the computer via the configuration software.
- Communication distance less than 200m.
- Easily temperature setting.
- Real time control screen.
- Curve records.
- Program selection.
- Alarm screen recording.
Products Parameters
Noted: Can provide customized services all types of equipment. Please consult us for details.
Model | SR-35N SR-35NS SR-35NH SR-35NSH | SR-50N SR-50NS SR-50NH SR-50NSH | SR-80N SR-80NS SR-80NH SR-80NSH | SR-125N SR-125NS SR-125NH SR-125NSH | SR-200N SR-200NS SR-200NH SR-200NSH |
Temp. range ℃ | -120~ 250°C setting the max temp according to the supplier heating or cooling source) -40~135°C (The maximum temperature range can be operated by using glycol water formula.) | ||||
SR-N | A set of cooling heat exchanger, heat exchanger, through proportional adjusting valve control cold heat into the heat exchanger, then through the uniform medium input to the reactor jacketed to do heat exchange and temp. Control, system has inside expansion tank. | ||||
SR-NS | Besides SR- N function,add one set heater used to reduce high temp. | ||||
SR-NH | Besides SR- N function,add electrical heating function | ||||
SR-NSH | Besides SR- N function,add one set heater used to reduce high temp and electrical heating function | ||||
Expansion tank | 100L | 200L | 280L | 390L | 500L |
Heat exchanger area | 3.5㎡ | 5㎡ | 8㎡ | 12.5㎡ | 20㎡ |
Electric heating function H | 25KW | 35KW | 50KW | 65KW | 80KW |
With “H” has heating function | |||||
Control mode | Feed forward PID + Our special dynamic control calculation,LNEYA PLC controller | ||||
Communication protocol | MODBUS RTU protocol,RS485 interface,optional Ethernet interface/R232 interface | ||||
Temperature control selection | Reactor material temperature control | ||||
Temperature feedback | The temperature of three points: the inlet and outlet of heat-conducting medium, material in reactor(External temperature sensor), PT100 sensor | ||||
Material temp. feedback:PT100 or 4~20mA or communication given Temp.feedback:PT100 | |||||
Process temp. feedback | |||||
feedback:PT100 | |||||
Temperature accuracy | ±1℃ | ±1℃ | ±1℃ | ±1℃ | ±1℃ |
Circulation pump | 200L/min 2.5BAR | 250L/min 2.5BAR | 400L/min 2.5BAR | 500L/min 2.5BAR | 750L/min 2.5BAR |
Input and display | 7-inch color touch screen,temperature graph display | ||||
Safety protection | Self-diagnosis function;freezer overload protection;high pressure switch;overload relay;thermal protection device;liquid low level protection;high temp. Protection and temp. fault protection. | ||||
Perform valve | Electric proportional control valve, control signal 4~20mA. | ||||
Piping material | SUS304 | ||||
Connection size | DN40 | DN40 | DN-50 | DN-65 | DN-80 |
Dimension cm | 150*120*185 | 180*140*240 | 180*140*240 | 220*180*265 | 220*180*265 |
Power AC380V50HZ | 2.3kw(max) | 3.5kw(max) | 4.5kw(max) | 8kw(max) | 10.5kw(max) |
With H power AC380V 50HZ | 27.3kw(max) | 38.5kw(max) | 54.5kw(max) | 73kw(max) | 90.5kw(max) |
Case material | Cold-rolled sheet spraying (standard color 7035) |