air cooled fluid cooler
Air-Cooled Fluid Coolers: Design, Operation, and Efficiency
Introduction
Air-cooled fluid coolers are essential in various industrial processes for their ability to maintain fluid temperatures. They operate by transferring heat from the fluid to the ambient air, ensuring the system operates within the desired temperature range. This article provides a detailed analysis of air-cooled fluid coolers, focusing on their design, operational efficiency, and maintenance for optimal performance.
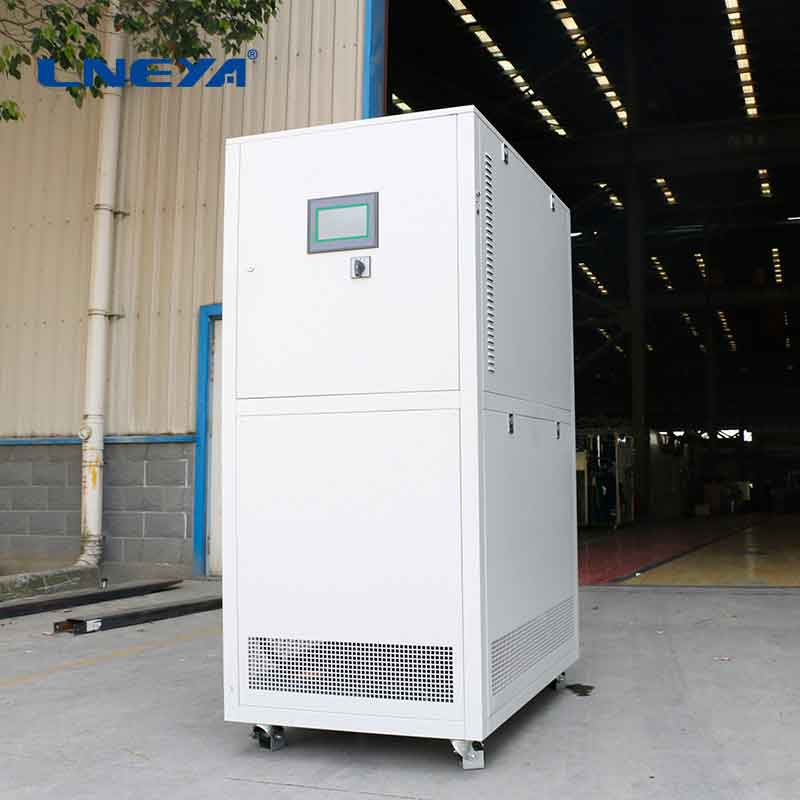
Design and Construction
Air-cooled fluid coolers consist of a heat exchanger coil, fans for airflow, and a structural frame. The coil is typically made of tubes with fins attached to enhance heat transfer. The design of the cooler, including the fin density (fins per inch) and coil construction (tube size and material), significantly affects its efficiency and performance.
Fin Density: Fins increase the surface area for heat transfer. Common fin densities include 8, 10, 12, and 14 fins per inch (FPI), with higher FPI values generally leading to better heat transfer but at the cost of increased air friction and power consumption.
Coil Construction: Coils can be constructed with different tube sizes (e.g., 5/8 in., 1/2 in., 3/8 in. OD tubes) and materials (copper, aluminum, or fin material). The choice depends on the application, with copper providing better heat transfer but at a higher cost.
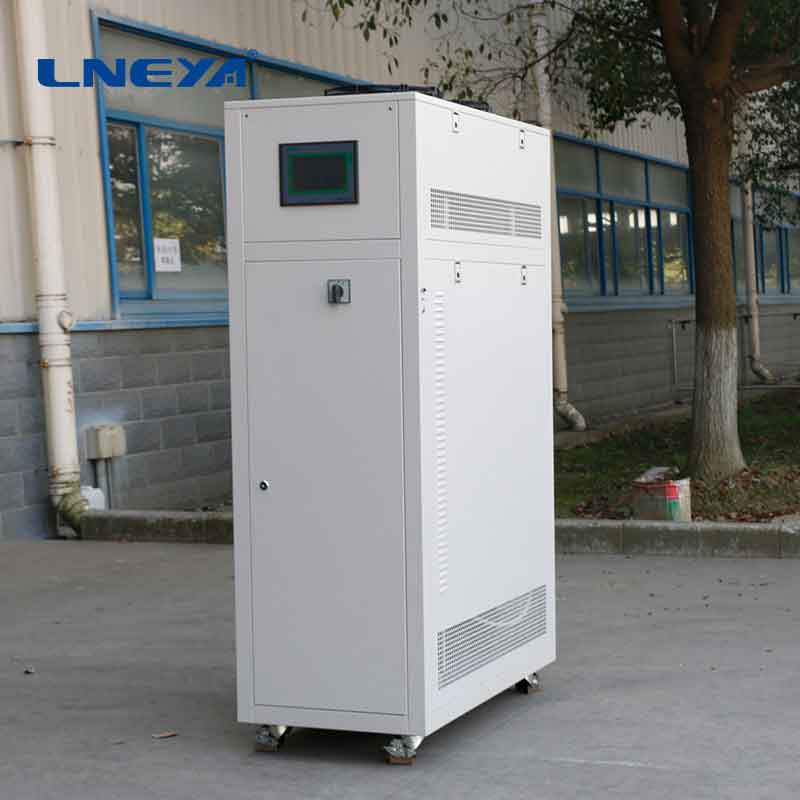
Operation
The operation of an air-cooled fluid cooler involves circulating the fluid through the coil, where heat is transferred to the ambient air. Fans push air over the coil fins, enhancing the heat transfer process. The efficiency of this process is influenced by:
Fan Configuration: Fans can be arranged in different lengths (e.g., 1 to 6 fans long) and can operate at different speeds (e.g., 700 RPM, 840 RPM, 1150 RPM). The configuration affects the airflow rate and the power required to drive the fans.
Coil Rows: Coils can be arranged in multiple rows (e.g., 3, 4, 6, or 8 rows deep). Deeper rows increase the heat transfer surface area but also increase the airside pressure drop, which affects fan power consumption.
Efficiency Optimization
Optimizing the efficiency of air-cooled fluid coolers involves several strategies:
Proper Sizing: Oversizing or undersizing can lead to reduced efficiency. Coolers should be sized based on the heat load and ambient conditions to ensure optimal performance.
Fan Control: Variable speed drives (VFDs) can modulate fan speed based on the cooling demand, reducing energy consumption when full capacity is not required.
Maintenance: Regular maintenance, including cleaning of the coil fins and replacement of worn fans, ensures sustained efficiency.
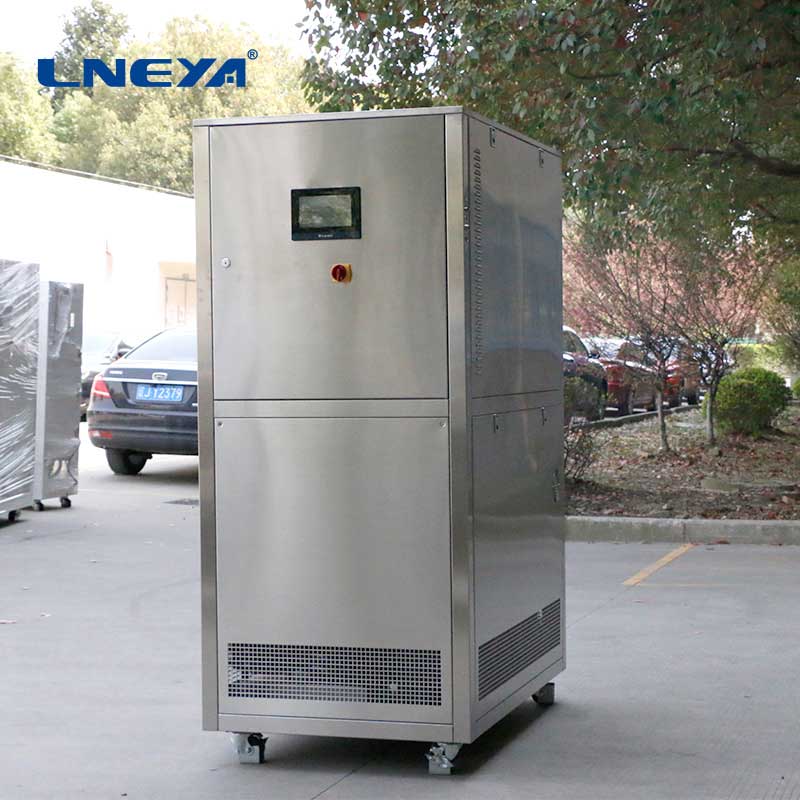
Maintenance Practices
Regular maintenance is crucial for the longevity and efficiency of air-cooled fluid coolers:
Inspections: Periodic inspections help identify potential issues such as leaks, worn fans, or malfunctioning controls.
Cleaning: Coils and fans should be cleaned regularly to prevent fouling from dust and debris, which can reduce heat transfer efficiency.
Replacement: Components like fans, motors, and gaskets should be replaced as they wear out to maintain optimal performance.
Conclusion
Air-cooled fluid coolers are vital for maintaining fluid temperatures in industrial processes. Their design, operation, and maintenance significantly impact their efficiency. By understanding the factors that influence performance and implementing proper maintenance practices, operators can ensure that their air-cooled fluid coolers operate efficiently and reliably. Regular inspections and cleaning, along with the use of advanced control strategies, contribute to the longevity and optimal efficiency of these coolers.
Related recommendations
industrial water chiller plant
547Introduction to Industrial Water Chiller Plants Industrial water chiller plants are essential for cooling processes in industries such as manufacturing, pharmaceuticals, and food processing. Th...
View detailssmall chiller plant
538Small Chiller Plants: A Comprehensive Overview Definition and Applications of Small Chiller Plants:Small chiller plants, also known as mini-chillers or pony chillers, are cooling systems design...
View details50 ton water chiller
35850 Ton Water Chiller: Medium-Scale Cooling Solutions for Commercial and Industrial Applications A 50-ton water chiller is an essential piece of HVAC equipment capable of managing significant th...
View detailsrefrigerant chiller system
411Refrigerant Chiller Systems: Efficient Cooling for Diverse Applications Refrigerant chiller systems are critical components in many industries and commercial facilities where precise temperatur...
View details
HelloPlease log in