circulating cooler
Circulating Cooler: Maintaining Constant Temperature in Industrial Processes
Circulating coolers, also known as cooling water circulators, are crucial for regulating temperatures in a variety of industrial and scientific applications. These systems circulate a coolant to maintain a consistent temperature, which is vital for processes such as chemical reactions, material testing, and temperature-sensitive manufacturing. This article provides an in-depth look at the principles, types, components, benefits, and the latest trends in circulating cooler technology.
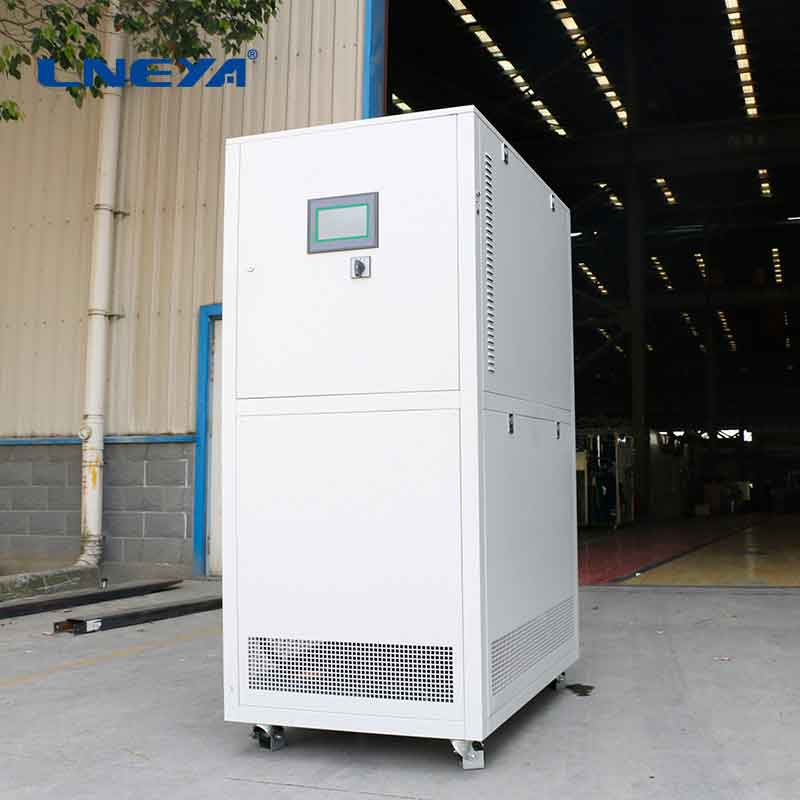
Principles of Operation
Circulating coolers operate on the principle of heat exchange. They use a coolant, typically water or a specialized fluid, which is circulated through a closed-loop system. The coolant absorbs heat from the process or equipment that needs cooling and then releases this heat to the environment through a heat exchanger or cooling tower.
Types of Circulating Coolers
There are several types of circulating coolers, each designed for specific applications:
Recirculating Chillers: These units are designed for applications requiring constant temperature control. They circulate coolant through a closed loop, maintaining a consistent temperature.
Portable Chillers: Compact and movable, these units are suitable for applications where flexibility and portability are needed.
Industrial Chillers: These are heavy-duty units designed for large-scale industrial processes that require continuous cooling.
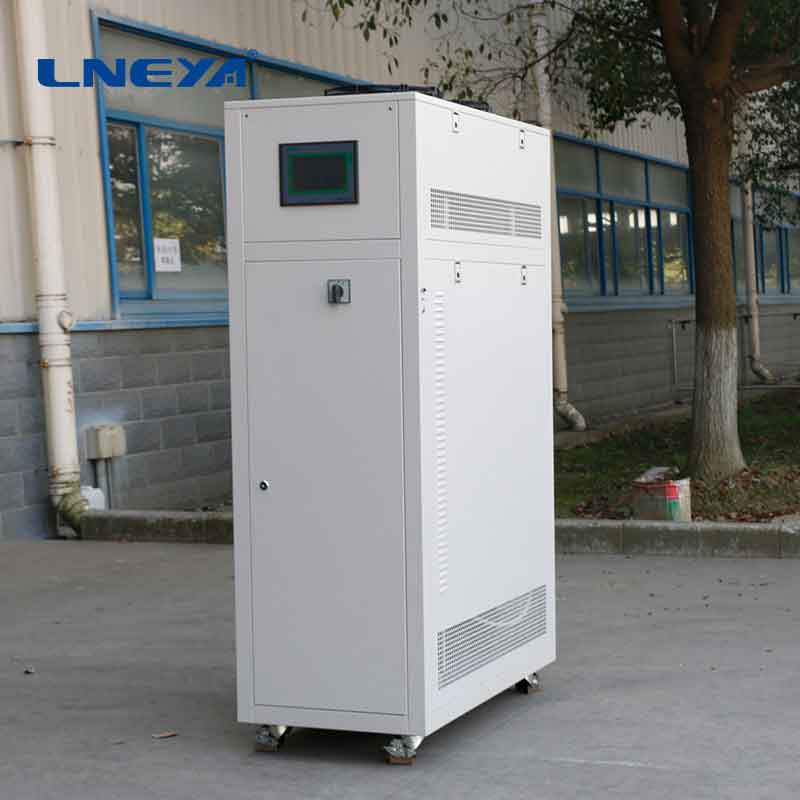
Components of a Circulating Cooler
The main components of a circulating cooler include:
Compressor: This is the heart of the chiller unit, responsible for circulating the coolant.
Heat Exchanger: This is where the coolant absorbs heat from the process fluid and releases it to the environment.
Pump: It circulates the coolant and process fluid within their respective loops.
Control System: This regulates the temperature by monitoring and adjusting the coolant flow and compressor operation.
Reservoir: Holds the coolant, which can be expanded or equipped with additional features like filtration or purification systems.
Benefits of Circulating Coolers
The use of circulating coolers offers several advantages:
Precision Temperature Control: Ensures consistent conditions for accurate and repeatable results.
Energy Efficiency: Modern chiller units are designed to minimize energy consumption, reducing operating costs.
Safety: Prevents overheating of processes and equipment, reducing the risk of accidents and damage.
Versatility: Suitable for a wide range of applications, from chemical reactions to cooling sensitive analytical instruments.
Latest Trends in Circulating Cooler Technology
Recent advancements in circulating cooler technology include:
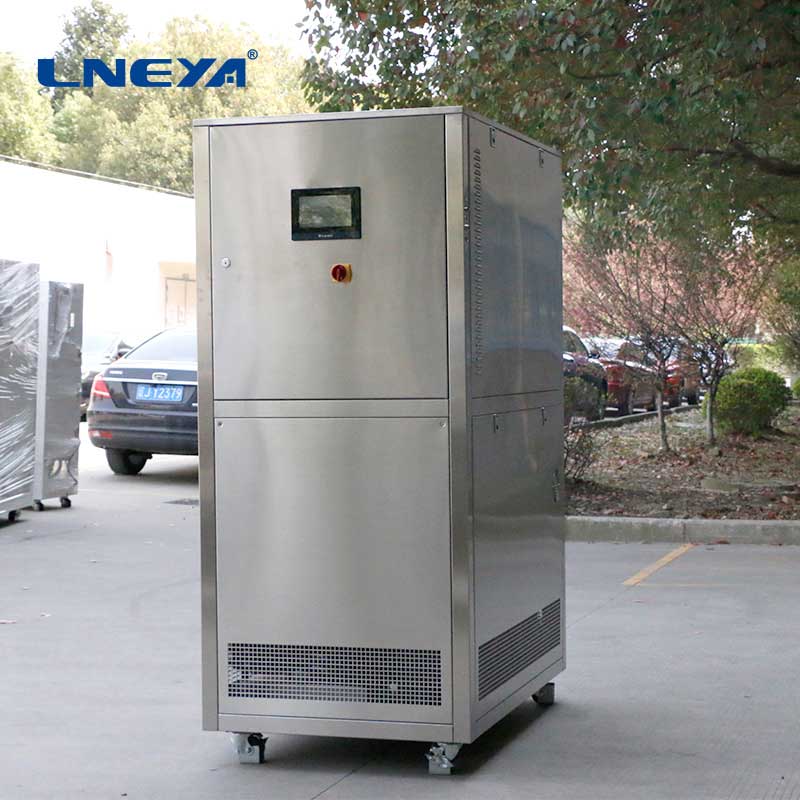
Solar-Powered Systems: As discussed in a review, these systems use solar energy to power the circulator, reducing electricity consumption and environmental impact.
Energy-Saving Evaluations: Comprehensive energy-saving evaluations, as highlighted in a study, help optimize the performance of cooling water systems, reducing energy consumption and costs.
Digital Controls: Advanced control systems provide more precise temperature regulation and user-friendly operation.
Integration with Smart Technologies: Smart sensors and IoT connectivity allow for remote monitoring and control, enhancing efficiency and convenience.
In conclusion, circulating coolers are indispensable in maintaining optimal conditions for various industrial processes and scientific experiments. By understanding their principles of operation, types, components, and the benefits they offer, industries can select the most suitable circulator for their needs. With the market showing steady growth and technology continuously evolving, circulating coolers will play a crucial role in the future of temperature control in various applications.
Related recommendations
What are the Hazards of Air in the Refrigeration System of Industrial Chillers?
1429What are the Hazards of Air in the Refrigeration System of Industrial Chillers? After the industrial chiller has been in operation for a long time, due to the corrosion of metal materials, th...
View detailschiller manufacturing company
357Chiller Manufacturing Company Chiller manufacturing companies play a pivotal role in today's industrial and commercial sectors by providing essential cooling solutions. These solutions are cruc...
View detailstypes of chiller system
528Introduction to Types of Chiller Systems Chiller systems are essential components of heating, ventilation, and air conditioning (HVAC) systems, providing cooling for commercial and industrial a...
View detailswater cooled chiller efficiency
514Water-Cooled Chiller Efficiency: Understanding the Advantages Water-cooled chiller systems are widely used in industrial and commercial applications for their ability to provide efficient and r...
View details
HelloPlease log in