glycol water cooling system
Glycol Water Cooling Systems: Design, Efficiency, and Maintenance
Introduction
Glycol water cooling systems are widely used in various industries for their ability to cool equipment effectively while operating in a wide range of ambient temperatures. These systems use a mixture of water and glycol, which lowers the freezing point of the water and provides protection against freezing. This article provides an in-depth analysis of glycol water cooling systems, focusing on their design, efficiency, and maintenance.
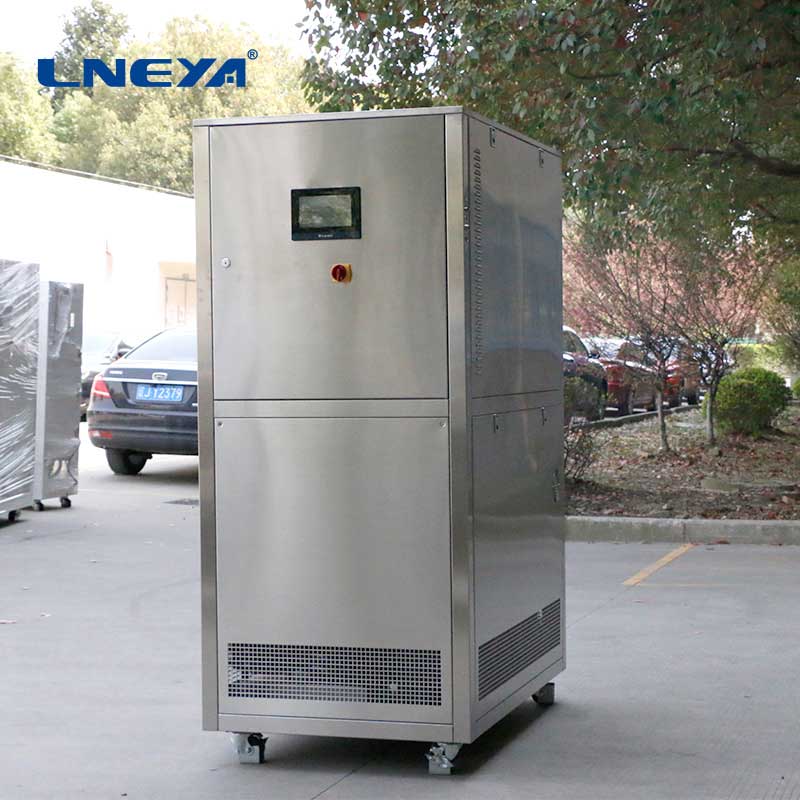
Design Considerations
The design of a glycol water cooling system involves several critical considerations:
Glycol Concentration: The concentration of glycol in the mixture is crucial. Too little glycol may not provide adequate freeze protection, while too much can reduce the heat transfer efficiency.
System Capacity: The system must be sized to handle the maximum heat load expected during operation.
Pump Selection: Pumps must be chosen to provide the necessary flow rate to meet the heat transfer requirements.
Heat Exchanger Design: The heat exchanger must be designed to maximize heat transfer between the glycol water mixture and the ambient air or other cooling mediums.
Components of Glycol Water Cooling Systems
A typical glycol water cooling system consists of:
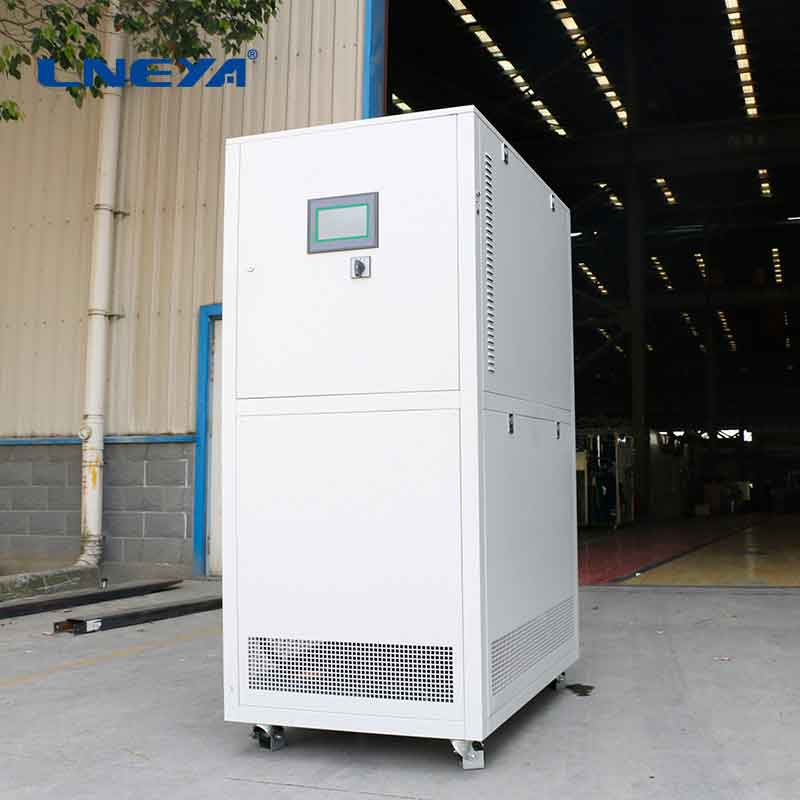
Chiller: The chiller produces the cold glycol water that is circulated through the system.
Pumps: Pumps circulate the glycol water mixture through the system.
Heat Exchanger: The heat exchanger transfers heat from the glycol water to the ambient air or another medium.
Reservoir: The reservoir stores the glycol water mixture and provides a location for air to be released from the system.
Controls: Controls regulate the operation of the chiller, pumps, and other components to maintain the desired temperature.
Efficiency Optimization
The efficiency of a glycol water cooling system can be optimized through:
Proper Sizing: Ensuring that all components are appropriately sized for the heat load and operating conditions.
Glycol Maintenance: Regularly testing and adjusting the glycol concentration to maintain optimal heat transfer properties.
Regular Maintenance: Cleaning and inspecting the system for any signs of wear or corrosion that could reduce efficiency.
Energy Management: Implementing energy management strategies, such as variable speed drives on pumps and scheduling systems for peak efficiency.
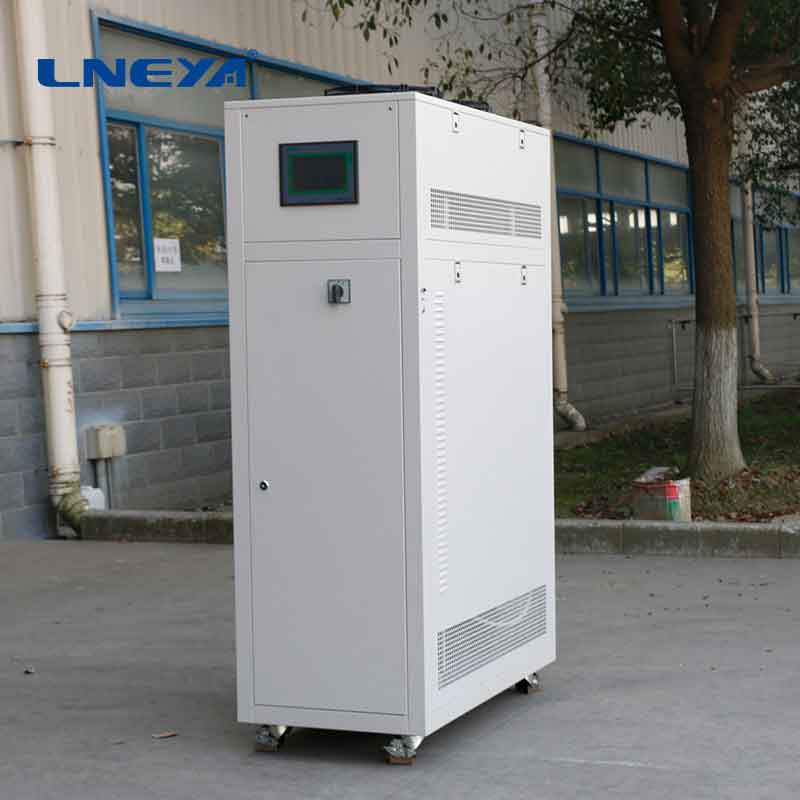
Maintenance Practices
Regular maintenance is essential for the longevity and efficiency of glycol water cooling systems:
Cleaning: Regularly cleaning the heat exchanger and other components to prevent fouling and maintain heat transfer efficiency.
Inspection: Periodic inspections to detect and rectify potential issues such as leaks or worn components.
Glycol Testing: Regularly testing the glycol for contamination, and replacing it as necessary to maintain the correct concentration and protect against corrosion.
Conclusion
Glycol water cooling systems are an effective solution for cooling applications in various industries. By understanding the design considerations, optimizing efficiency, and implementing proper maintenance practices, operators can ensure that their glycol water cooling systems operate efficiently and reliably. Regular inspections and cleaning, along with the use of advanced control strategies, contribute to the longevity and optimal efficiency of these systems.
Related recommendations
water cooled chilling plant
5215hp Chiller: Mid-Range Cooling Solutions for Diverse Applications A 5hp chiller is a mid-scale cooling system designed for applications that require up to 3.7 kW of cooling capacity. These chil...
View detailsPerformance Characteristics of Chiller
1412Performance Characteristics of Chiller The primary concern of users when purchasing a chiller is the quality and cooling effect of the chiller, so how do we know whether a chiller is good or ...
View detailsevaporator of chiller
365Definition and Function of Evaporator in Chiller Systems The evaporator is a vital part of a chiller system, where the heat absorption process occurs. It is positioned on the low-pressure side ...
View detailscooling systems uk
183Cooling Systems in the UK: A Comprehensive Guide IntroductionCooling systems play a crucial role in various sectors across the UK, from industrial manufacturing to commercial and residential bu...
View details
HelloPlease log in