process cooling water systems
Process cooling water systems play a vital role in maintaining the efficiency and safety of industrial processes. These systems are designed to absorb and remove excess heat from processes, preventing equipment overheating and ensuring consistent product quality. They are an integral part of many industries, including manufacturing, chemical processing, food and beverage production, and power generation.
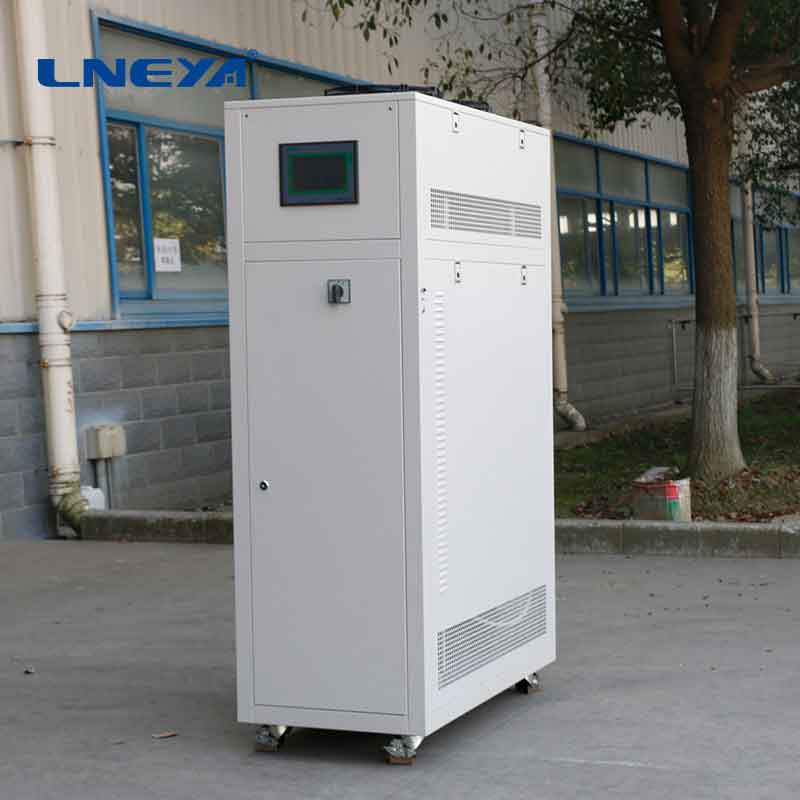
Principles of Operation:
Process cooling water systems operate on the principle of heat transfer. Water, due to its high specific heat capacity, is an effective coolant. When water comes into contact with equipment or processes generating heat, it absorbs the heat and increases in temperature. The warmed water is then circulated back to a heat exchanger or cooling tower where it releases the heat, either to the atmosphere or to a secondary cooling medium.
Components of Process Cooling Water Systems:
The basic components of a process cooling water system include:
Cooling Tower: This is where the majority of the heat rejection occurs. Cooling towers use atmospheric air to cool the water, either through evaporative cooling or dry cooling methods.
Pumps: Pumps are used to circulate water through the system, maintaining the necessary flow rate to absorb and remove heat.
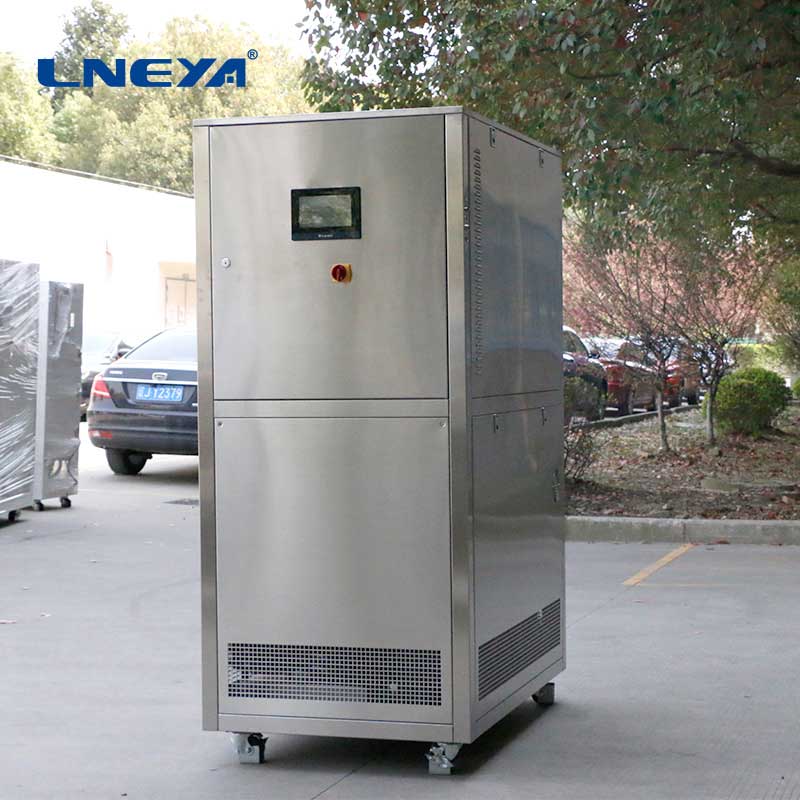
Heat Exchangers: These are used to transfer heat from the process fluid to the cooling water, reducing the process fluid temperature.
Pipework and Valves: A network of pipes and valves is used to direct the flow of water throughout the system.
Controllers and Instruments: These monitor and control the temperature and flow of the cooling water, ensuring optimal performance.
Applications of Process Cooling Water Systems:
Process cooling water systems are used in a variety of industrial applications, including:
Manufacturing: In various manufacturing processes, such as plastic injection molding and metalworking, where machines and processes generate heat that needs to be controlled.
Chemical Processing: In chemical reactions, where temperature control is critical for reaction rates and product quality.
Food and Beverage Production: For processes like pasteurization, fermentation, and freezing, where consistent temperatures are essential for food safety and quality.
Power Generation: In power plants, particularly in cooling the condensers used in steam turbine cycles.
Considerations for Process Cooling Water Systems:
When designing and maintaining process cooling water systems, several factors must be considered:
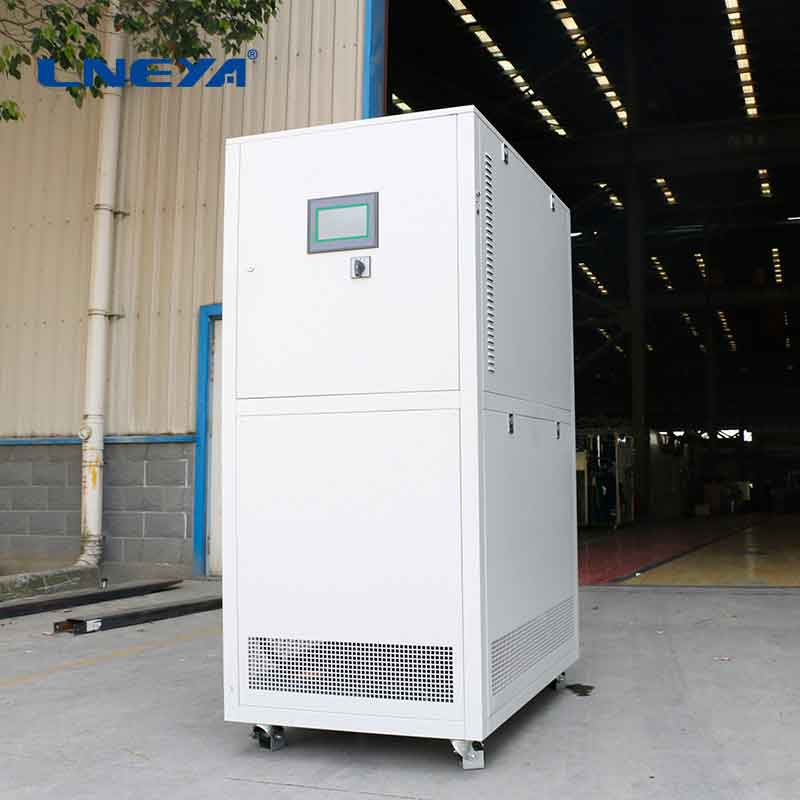
Corrosion: Water can be corrosive to metal components, so materials resistant to corrosion, such as stainless steel or specialized alloys, may be used.
Scale Formation: Minerals in the water can lead to scale formation, which reduces heat transfer efficiency. Water treatment programs are often implemented to prevent scaling.
Microbiological Growth: Bacteria, algae, and fungi can grow in cooling water systems, leading to fouling and other issues. Regular cleaning and the use of biocides may be necessary.
Energy Efficiency: The efficiency of the cooling system directly impacts energy consumption. Modern systems use variable speed drives on pumps and fans, as well as other energy-saving technologies.
Environmental Impact: The use of water in cooling systems must be balanced with environmental considerations, such as water conservation and the discharge of heated water into waterways.
Conclusion:
Process cooling water systems are critical components of many industrial operations. They ensure that processes run efficiently and equipment operates within safe temperature ranges. As industries continue to evolve, the design and operation of these systems must keep pace with new challenges, such as environmental regulations and the need for greater energy efficiency. By understanding the principles of operation and the factors that affect performance, engineers and operators can optimize their process cooling water systems for maximum efficiency and reliability.
Related recommendations
chiller evaporator
146Chiller Evaporator: A Comprehensive ExplanationThe chiller evaporator is a crucial component within a chiller system, playing a fundamental role in the refrigeration process. As an essential part...
View detailsindustrial chiller units for sale
471Industrial Chiller Units for Sale: An In-Depth Overview Industrial chiller units are indispensable in numerous industries for maintaining optimal temperatures in processes such as chemical proc...
View detailsindustrial water chiller singapore
369Industrial Water Chiller Systems in Singapore: Market Growth and Sustainability Industrial water chiller systems are critical components in Singapore's industrial sector, providing essential co...
View detailsconstant temp water bath
435Introduction to Constant Temperature Water BathA constant temperature water bath, also known as a thermostatic water bath, is a crucial piece of laboratory equipment used to provide a stable tempe...
View details
HelloPlease log in