closed cooling water system
Closed cooling water systems, also known as closed recirculating water systems, play a critical role in various industrial applications by providing a controlled environment for heat exchange processes. These systems are designed to circulate water within a closed loop, where the water is continuously cooled or heated and then reused, thereby optimizing water usage and reducing environmental impacts.
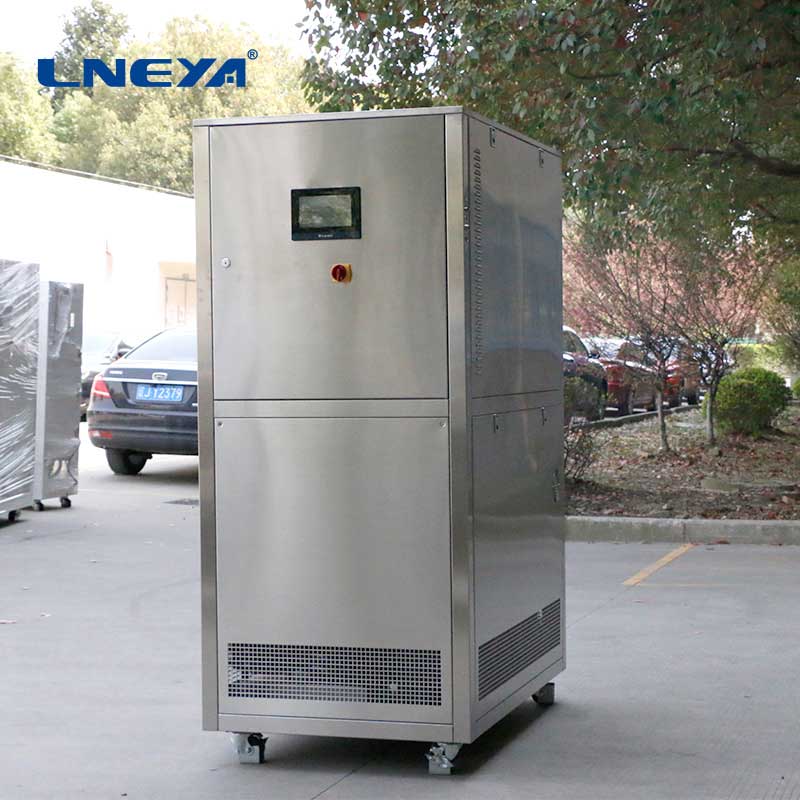
Advantages of Closed Cooling Water Systems:
Closed cooling water systems offer several advantages over open systems. They provide better control over water quality and temperatures, which is essential for sensitive industrial processes. The small requirement for makeup water simplifies the management of potential waterside problems such as scaling and biological fouling. Since evaporation is minimal or nonexistent in closed systems, high-quality water can be used for makeup, reducing the risk of scale formation and corrosion.
Limitations of Closed Cooling Water Systems:
Despite their benefits, closed cooling water systems also have certain limitations. The continuous recirculation of water can lead to the accumulation of contaminants over time, affecting water quality. Scaling and corrosion can still be issues if the system is not properly maintained and treated. Additionally, closed systems may have higher initial costs due to the need for specialized equipment and controls, and they may consume more energy for pumping and cooling compared to open systems.
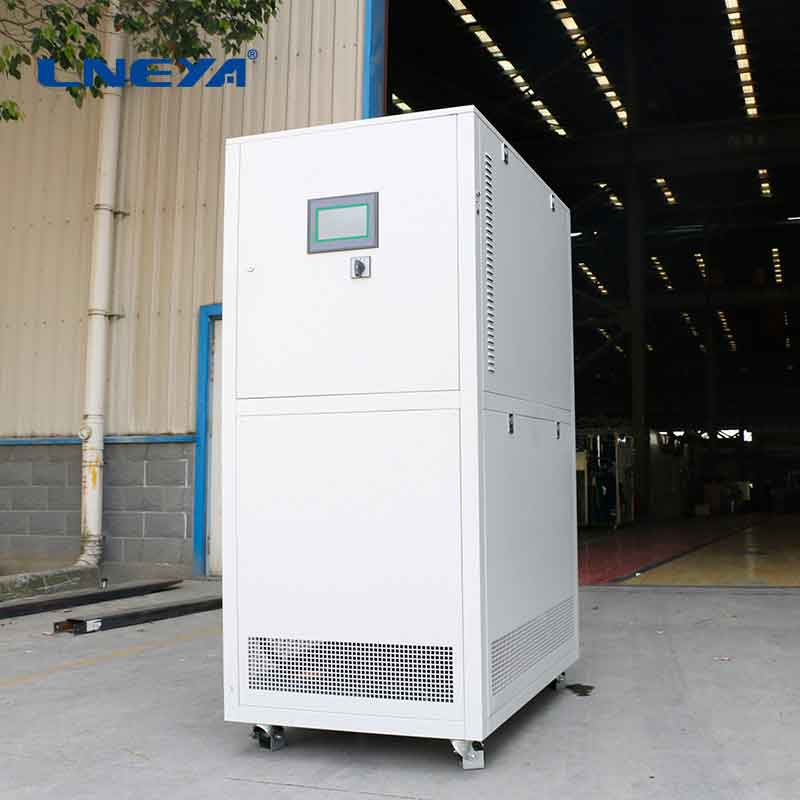
Components and Operation:
Closed cooling water systems typically include components such as heat exchangers, pumps, and sometimes cooling towers or chillers. The water circulates through the system, absorbing heat from processes and transferring it to the cooling medium, which then dissipates the heat to the atmosphere. In some cases, closed systems may be part of a larger primary cooling circuit, serving as auxiliary systems for specific pieces of equipment or processes.
Treatment and Monitoring:
Proper treatment and monitoring are crucial for the efficient operation of closed cooling water systems. Treatment programs aim to control corrosion, scale, and microbiological fouling. Common treatment methods include the use of corrosion inhibitors such as chromate, molybdate, or nitrite. These inhibitors form a protective layer on metal surfaces, preventing corrosion. However, the choice of inhibitor may be influenced by factors such as the type of metals in the system, water chemistry, and environmental regulations.
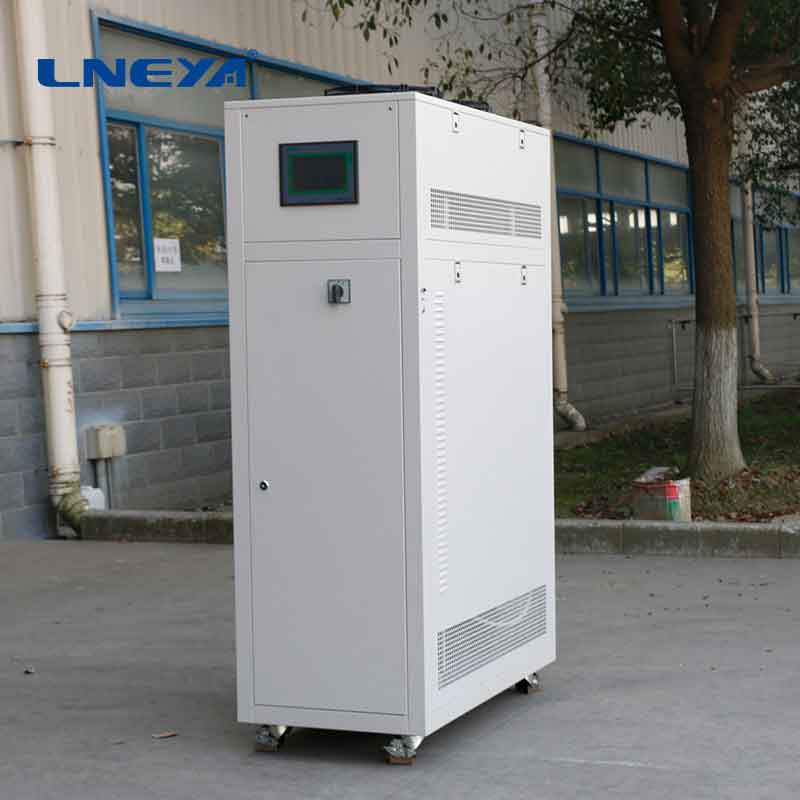
Monitoring of closed cooling water systems involves regular testing of water samples to ensure that treatment chemicals are within the desired parameters. Parameters such as pH, conductivity, and levels of corrosion inhibitors are typically monitored to maintain optimal water quality. Advanced monitoring systems may also include real-time sensors for continuous tracking of critical parameters.
Conclusion:
Closed cooling water systems are an essential part of many industrial processes, providing precise temperature control and efficient water use. While they offer significant advantages, they also require careful management to prevent issues such as contamination, scaling, and corrosion. By implementing proper treatment programs and monitoring practices, industries can ensure the reliability and longevity of their closed cooling water systems, contributing to sustainable water management practices.
Related recommendations
recirculating water cooling system
487Recirculating water cooling systems are widely used in various industrial applications, particularly in the oil and gas sector, where they play a critical role in maintaining optimal operating tem...
View detailswater cooling water
381Water Cooling Water: Efficient Heat Management in Various Applications Water cooling systems have long been a preferred method for managing heat in various applications due to water's inherent ...
View detailschiller layout
70Chiller Layout: A Comprehensive GuideIn the realm of cooling systems, a well - designed chiller layout is crucial for the efficient, reliable, and safe operation of chillers. Whether for commerci...
View detailsheater for oil tank
576Heater for Oil Tank: Maintaining Temperature in Oil Storage Oil tanks, especially in the oil and gas industry, require heaters to maintain the oil's temperature and ensure its proper flow. Heat...
View details
HelloPlease log in