water cooled chiller maintenance
Water-Cooled Chiller Maintenance: A Guide to Ensuring Efficiency and Longevity
Water-cooled chillers are vital components in many industrial and commercial HVAC systems, providing essential cooling for processes, equipment, and buildings. To maintain their optimal performance, efficiency, and longevity, it’s crucial to implement a comprehensive maintenance program. This guide outlines the key aspects of water-cooled chiller maintenance, including daily logs, cleaning, inspections, and preventive measures.
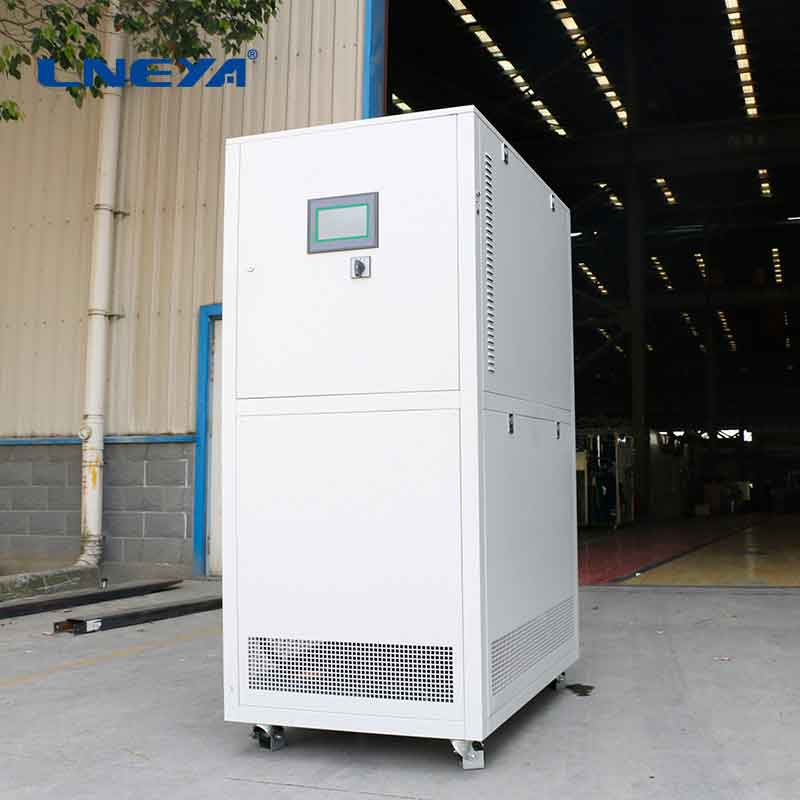
Daily Logs and Monitoring
Daily monitoring of the chiller’s operation is the first line of defense in maintaining its performance. Logging essential data such as temperatures, pressures, and fluid levels can help predict and prevent potential issues before they escalate. Key parameters to monitor include:
Condensation pressure/temperature
Evaporation pressure/temperature
Water flow rate and inlet/outlet water temperatures
Suction temperature for all compressors
Discharge temperature for all compressors
Oil temperature and pressure, acidity, and humidity
Inspection and Cleaning
Regular inspections are necessary to identify any signs of wear, corrosion, or leaks. Visual checks should be performed to ensure all equipment is operating correctly and safety systems are in place. Key inspection tasks include:
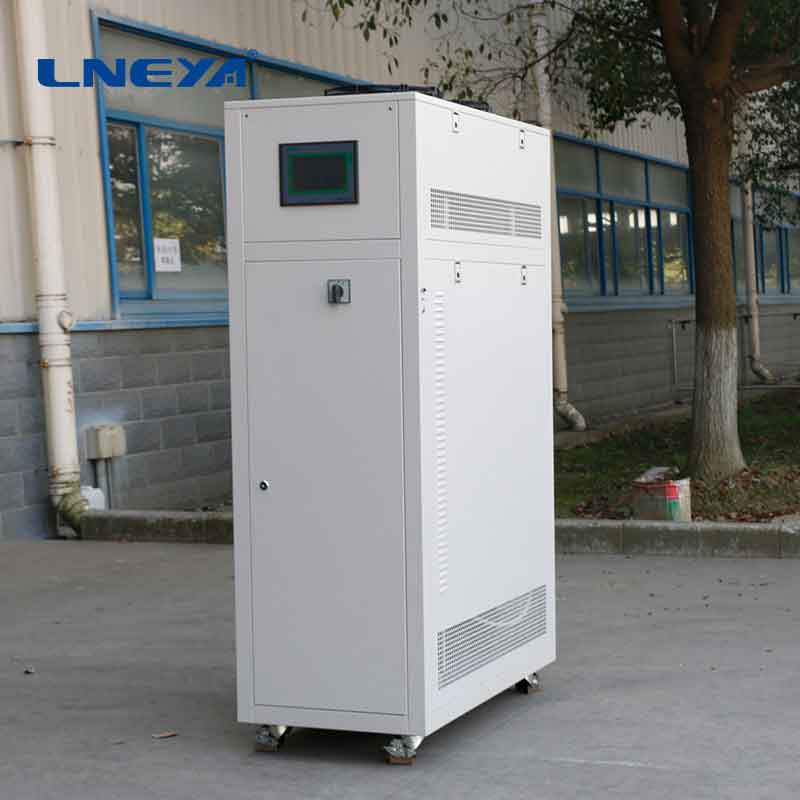
Checking for leakages in water and refrigeration pipeworks
Detecting sources of abnormal vibrations and unusual sounds
Inspecting chiller components for corrosion, especially pipework and electrical connections
Cleaning or replacing air and water filters to maintain proper airflow and water flow
Preventive Maintenance Tasks
Preventive maintenance involves a series of tasks performed at regular intervals to keep the chiller in good working condition. These tasks include:
Chemically washing condenser coils annually to remove scale and other deposits
Changing oil filters and oil as recommended by the manufacturer
Purging the system of non-condensable gases to maintain efficiency
Analyzing compressor oil annually to detect contamination and determine the need for oil changes
Inspecting motors and starting mechanisms, including sensor calibration and microprocessor control inspection
Best Practices for Maintenance
To ensure the chiller operates at peak efficiency and longevity, follow these best practices:
Keep Tubes Clean: Regularly clean the condenser and evaporator tubes to maintain heat transfer efficiency. Even a small amount of scale can significantly increase energy costs.
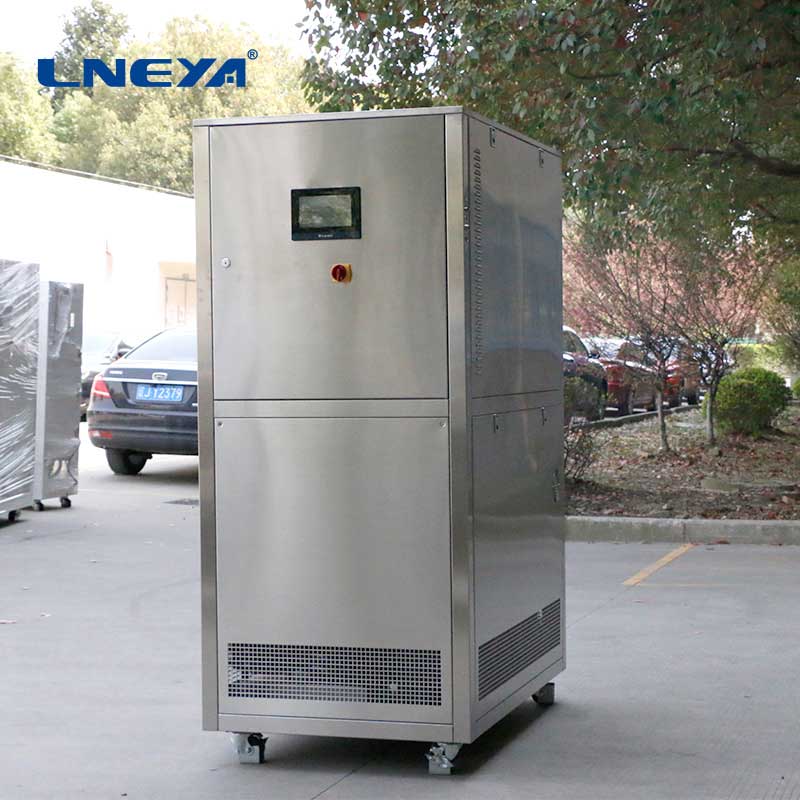
Ensure a Leak-Free Unit: Regularly check for refrigerant leaks to prevent system damage and environmental hazards. Monitor refrigerant levels and conduct frequent leak checks.
Maintain Proper Water Treatment: A proper water treatment program can help reduce the buildup of contaminants on heat transfer surfaces and slow the growth of harmful bacteria.
Control the Flow: Ensure the chilled water flow rate is within the recommended range to prevent laminar flow or excessive vibration and noise, which can lead to tube erosion.
Install Variable Speed Drives: Variable speed drives can help optimize the chiller’s performance by adjusting the flow rate based on the load demand, resulting in energy savings.
Develop a Maintenance Plan: Create a regular maintenance plan based on the manufacturer’s recommendations and your facility’s specific needs. Use a computerized maintenance management system (CMMS) to streamline the process and ensure timely maintenance tasks are performed.
By adhering to a comprehensive maintenance program that includes daily monitoring, regular inspections, and preventive maintenance tasks, you can ensure the efficiency, safety, and longevity of your water-cooled chillers. This proactive approach will minimize downtime, reduce energy costs, and protect your investment in these critical HVAC systems.
Related recommendations
freeze chiller
275Introduction to Freeze Chillers Freeze chillers, also known as freezing chillers, are unique cooling systems that utilize the freezing process of a refrigerant to achieve cooling. These systems...
View detailsLaboratory Refrigeration and Heating Constant Temperature Circulation System
1226Laboratory Refrigeration and Heating Constant Temperature Circulation System The laboratory heating and cooling cycle thermostat uses various media with different temperatures to perform hig...
View detailston chiller
390What is a Ton Chiller? A ton chiller is a refrigeration system designed to remove heat from water or other liquids, with its cooling capacity measured in tons. One ton of cooling capacity is eq...
View detailsWhat should be done if the compressor of an chiller industrial is burned out?
969What should be done if the compressor of an chiller industrial is burned out? 1. The reason for the burning of the LC -25 ~ -5°C Water Chillers compressor may be due to a lack of phase ...
View details
HelloPlease log in